Hanryk® Casting Services
Our Metal Casting Service
For over 16 years, Hanryk® has been providing custom metal casting services for a variety of industries and project types. Our in-house mold-making, heat treatment, and precision casting services bring experience and quality to every project.
If you’re searching for the right partner for your high-volume metal casting project, the Hanryk is a metal casting foundry partner you can trust. We can help you produce the perfect metal parts and components with a proven casting process. During mold making, the molten metal is poured and not forcibly injected, mold casting, delivering the best lead times and costs.
Our product capabilities range from prototyping custom projects to large run automotive, aerospace, and railway projects.
Materials For Casting
Carbon Steel
Alloy Steel
Stainless steel
Aluminum
Copper
- Casting Tolerance: ISO 2768-mK, VDG P690 D1-D2
- Casting Roughness: Ra1.6-Ra3.2
- Casting Weight: 0.005kg – 50kg
- Material Standard: GB, ASTM, AISI
ISO 2768-mK, VDG P690 D1-D2
Ra1.6 – Ra3.2
0.005kg – 50kg
GB, ASTM, AISI
Aluminum Die Casting Capabilities
Low Pressure Die Casting
Low Operation Cost
No Porosity
With Heat Treatment & Surface Treatment
Good Metal Liquid Flow Stability
- Pressure: ≤0.15 Mpa
- Mold Life: Long Mold Life
- Mold Cavity Type: Metal/Sand
- Part Size: Small/medium/large
≤0.15 Mpa
Long Mold Life
Metal/Sand
Small/medium/large
Let's start a project today!
24/7 Engineering Support.
A quick & attractive quote within 6 hours.
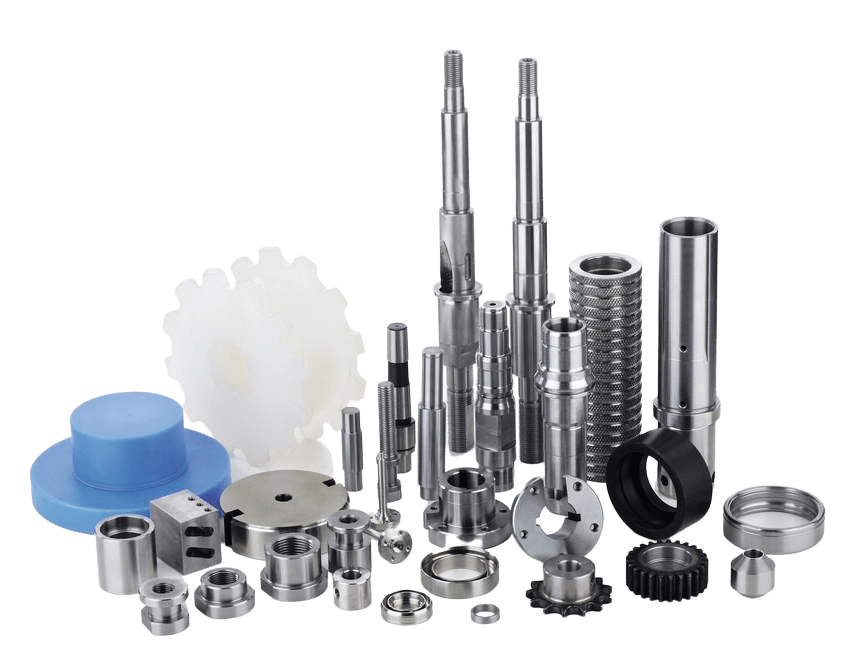
What is Investment Casting?
The investment casting process is a refined technique for the casting of alloy materials. Mold making, the first step in the process, involves the use of waxes to create patterns that are “invested” with refractory materials. The alloy is then poured into a cavity (mold) in the refractory material in order to produce a duplicate of the pattern as the desired part. This age-old industrial process has the power and reliability to provide tolerances within thousands of an inch.
The modernization of investment casting techniques within foundries has been perfected over decades of modern industrialization. Pricing varies per metal and market prices, but investment casting delivers the best cost-per-part scenario over other options.
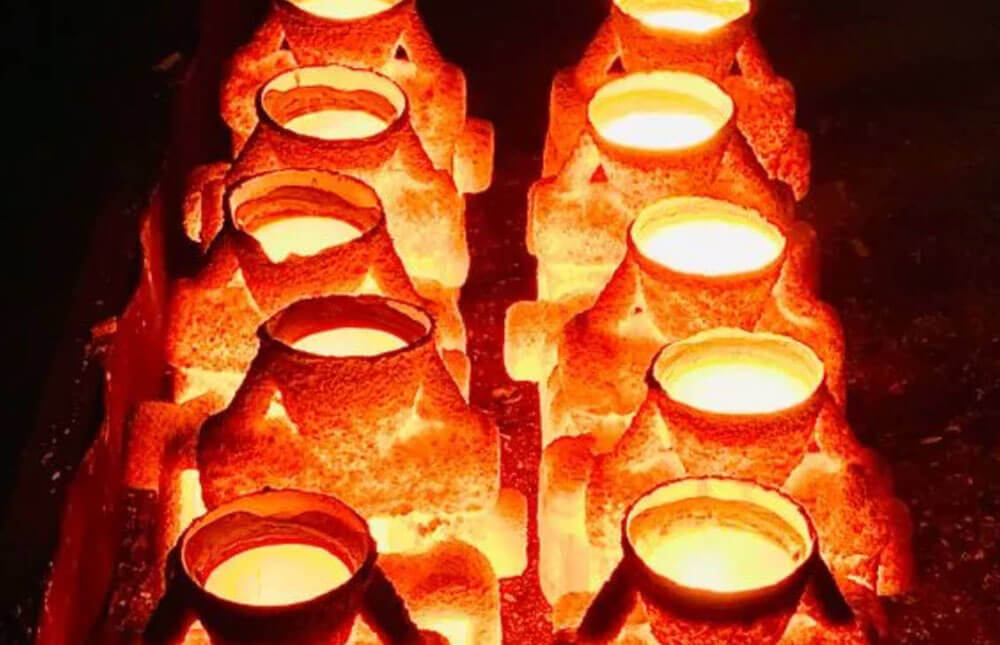
The Investment Casting Process
At Hanryk®, our investment casting foundry is capable of producing a wide range of complex and precision shapes. By heating the material above its melting point and pouring it into the mold, it will solidify into the required shape.
- Pattern produced – An original pattern is made from wax, plastic, 3D printing filament or another material.
- Mold preparation – A mold is manufactured from aluminum alloy, chosen for its low price, low melting point and lightweight.
- Wax model and tree assembly – Wax is injected into the alloy mold, with a tree-like structure assembled, dried and sprayed with sand.
- Sand shell and dewaxing – The mold is repeatedly coated in refractory material, before being heated and dewaxed.
- Material pouring – The material is poured into the dewaxed sand shell, which is then broken by hand or machine.
- Machining – The final investment cast part is cut, polished, and machined according to its intended purpose.
- Testing – The blank parts are tested for defects, and possibly machined further to create the final product.
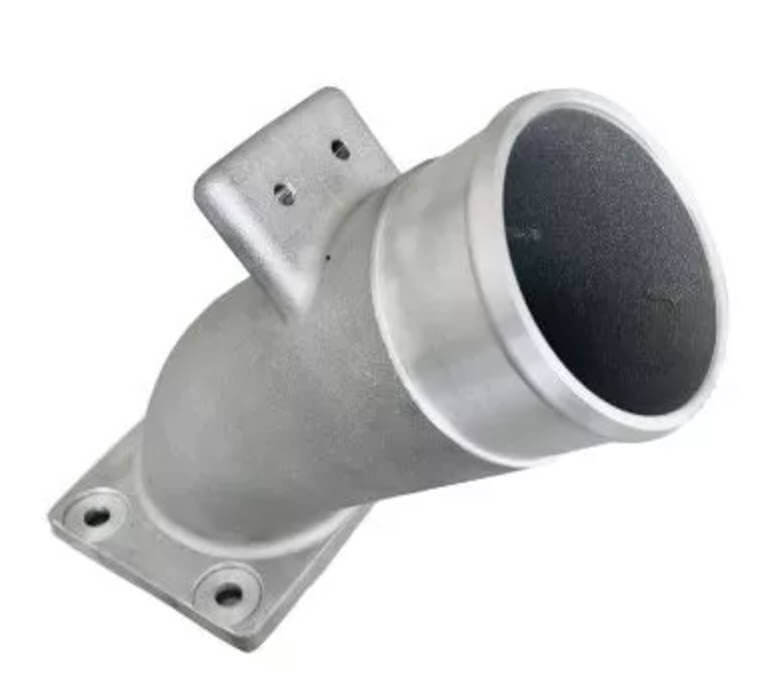
Advantages of Investment Casting
Also known as lost-wax casting, investment casting is widely regarded for its accuracy and integrity. While this process has been around for hundreds of years, technological advancements continue to improve quality outcomes and tolerances. Along with producing accurate parts and components, the advantages of investment casting include versatility is across industries and repeatable across production iterations.
Aluminum Die Casting Advantages
Die casting is ideal for large order quantities and large-scale pieces because it delivers consistency and repeatability. Our aging treatment aims to eliminate internal stress, stabilize structure and size, and improve mechanical properties. Our laboratory is a constant temperature laboratory to ensure accuracy.
Aluminum die casting delivers ideal tolerance control and surface finish with high volume capacity. The quenching transfer time is less than 15 seconds, delivering consistently precise die cast parts.
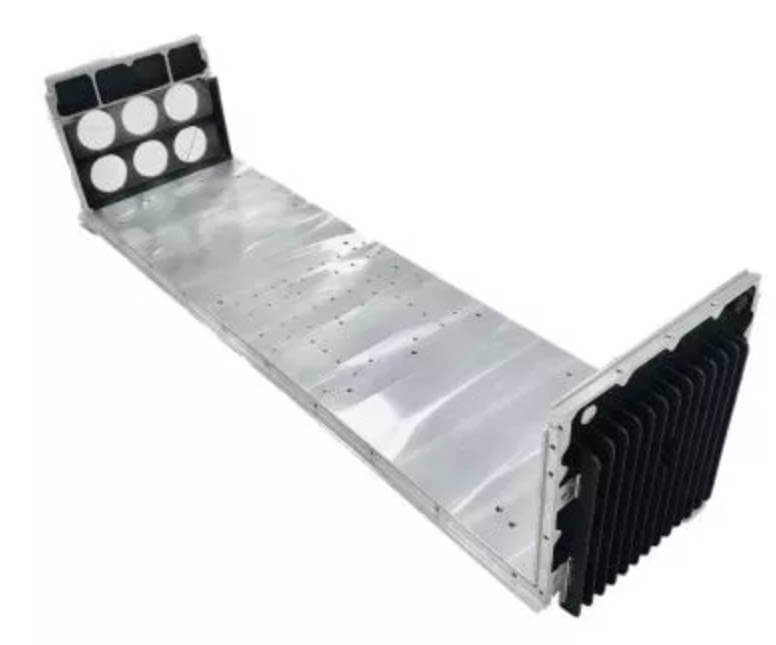
VARIOUS INDUSTRIES
With 16+ years of manufacturing experience, Hanryk offers the best solutions for all rapid prototyping and low-volume manufacturing needs.